
تولید شمش منیزیم
تولید شمش منیزیم : کاربرد منیزیت و اكسيد منيزيم (DBM CCM)
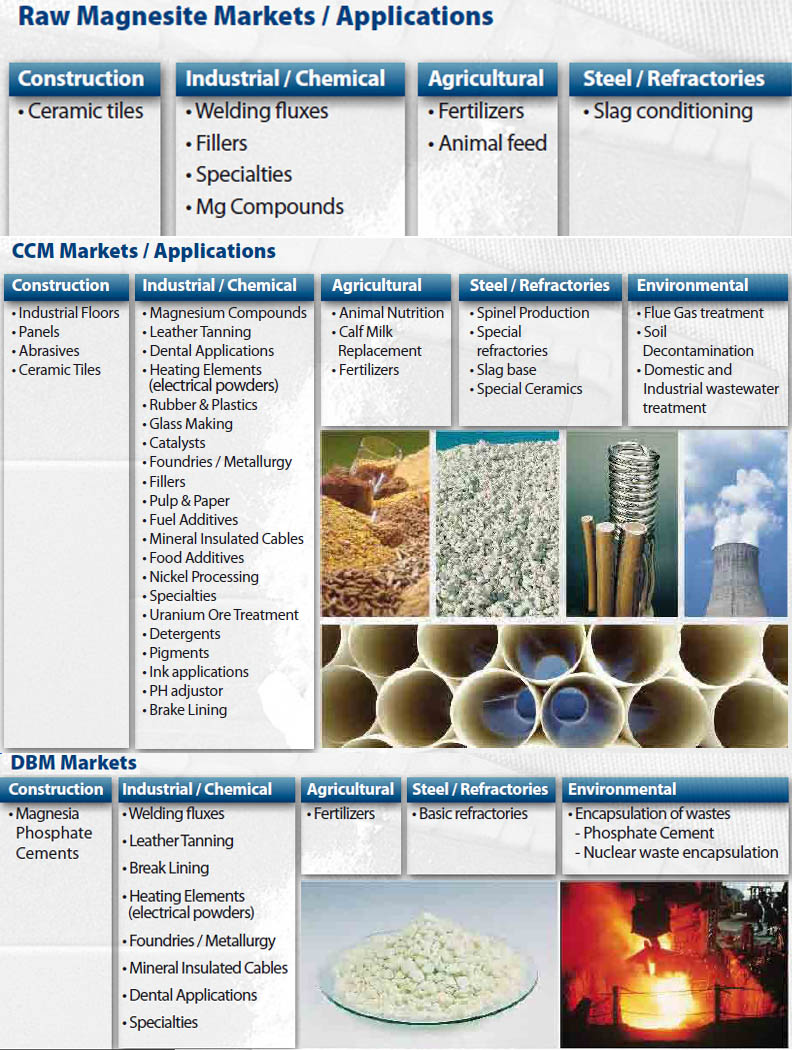
تولید شمش منیزیم : منیزیت کانیای است که نقش اصلی را در صنایع دیرگداز و نسوز دارد. فرآوردههای منیزیتی، به طور عمده شامل دیرگدازها میباشند که در بخش صنایع دیرگداز به فراوانی استفاده میشود. بخش دیگری از این فرآورده ها، در مصارف کشاورزی، داروسازی، شیمی و ... بهکار برده میشود. امروزه فولادسازی مدرن و درحال توسعه، نیاز به افزایش تولید دیرگدازهای منیزیتی با کیفیت بالا دارد.
منیزیت کاملا تکلیس شده، شامل بلورهای پریکلاز در یک زمینهی بلورین دانه ریز میباشد و نقطهی ذوب آن، 2800 درجه سانتیگراد و وزن مخصوص آن 6/3 گرم بر سانتیمترمکعب است. برای افزایش مقاومت گرمایی و پایداری فرآوردههای منیزیتی، 5 تا 12 درصد آلومین افزوده میشود که این عمل منجر به تشکیل یک فاز اسپنیلی از MgO میگردد.
ذخیره و تولید جهانی منیزیت:
ذخایر قطعی منیزیت دنیا، 5/2 و ذخایر پایهای آن 4/3 میلیارد تن میباشد. تولید سالانه منیزیت در سطح دنیا در حدود 20 میلیون تن است که از این مقدار، بیشترین سهم مربوط به کشورهای تازه استقلال یافتهی شوروی، چین، کره شمالی، چک و اسلواکی بوده است. کشورهای اصلی تولیدکننده استرالیا، یونان، ترکیه، اسپانیا، برزیل، یوگوسلاوی، هند و کانادا هستند.
تولید شمش منیزیم - تولید شمش منیزیم ، انواع تولید شمش منیزیم
تولید شمش منیزیم
تولید شمش منیزیم - منیزیم فلزی است به رنگ سفید یا نقرهای با نماد Mg، عدد اتمی ۱۲، وزن اتمی ۲۴٫۳۰۵۰ و ساختار بلور آن شش گوش یا هگزاگونال متراکم است. نام منیزیم از واژه ی یونانی Magnesia حوضهای در Thessaly یا از نام شهر قدیمی Magnesia در آسیای صغیر گرفته شدهاست. منیزیم هشتمین عنصر فراوان در پوسته زمین و سومین عنصر فراوان و محلول در آب دریاست.
منیزیم در گروه دو (IIA) جدول تناوبی به عنوان فلز قلیایی خاکی قرار دارد.
منیزیم به عنوان سبکترین فلز صنعتی با ویژگیهای منحصر به فرد متالورژیکی، کاربردهای وسیعی در صنایع مختلف یافتهاست. علیرغم وجود محدودیتهای ذاتی در تولید و استفاده از منیزیم به دلیل این ویژگیها روز به روز به کاربرد این فلز در صنایع مختلف افزوده میشود. میتوان از ویژگیهای منحصر به فرد منیزیم موارد زیر را برشمرد:
منیزیم با چگالی ۱٫۷ گرم بر سانتیمتر مکعب، سبکترین فلز با قابلیت تولید قطعات صنعتی میباشد. چگالی منیزیم ۳۰ درصد از آلومینیوم کمتر (چگالی آلومینیوم ۲٫۷ گرم بر سانتیمتر مکعب) و تنها ۲۰ درصد چگالی آهن است (چگالی آهن ۷٫۸ گرم بر سانتیمتر مکعب). این ویژگی منحصر به فرد جذابیت فراوانی برای استفاده از این فلز در تولید قطعات متحرک و صنعت حمل و نقل ایجاد کردهاست.
همراه با چگالی پایین، آلیاژهای منیزیم استحکام قابل توجهی از خود نشان میدهند. این ویژگی سبب افزایش نسبت استحکام به وزن این فلز شدهاست. به عنوان مثال جهت تغییر جنس تیری ۱۰ کیلویی از فولاد، میتوان بدون تغییر چقرمگی از تیری منیزیمی با وزن ۳٫۸ کیلوگرم استفاده کرد. نسبت بالای استحکام به وزن سبب شده در بسیاری از قطعات مختلف صنایع هوایی و خودروسازی از منیزیم استفاده شود. نمونه چنین قطعاتی پوسته جعبه دنده هلیکوپتر میباشد.
از ویژگیهای دیگر آلیاژهای منیزیم میتوان به قابلیت جذب ارتعاشات توسط این فلز اشاره کرد. این ویژگی سبب شده استفاده از آلیاژهای منیزیم برای مدیریت ارتعاشات مخصوصاً در صنعت خودرو بسیار مورد توجه قرار گیرد. در مقایسه با آلیاژ آلومینیوم A356 با ضریب میرایی ۱٪ در تنش ۱ مگا پاسکال، برای آلیاژ AZ91 منیزیم این ضریب ۲۵٪ میباشد. در تنش ۱۰۰ مگا پاسکال این ضریب برای آلومینیوم A356 %4 و برای منیزیم AZ91 %54 میباشد.
علاوه بر قابلیت میرایی ارتعاشات، منیزیم سپری قوی در برابر امواج الکترو مغناطیس نیز میباشد. دیوارهای ۱ میلیمتری از منیزیم به راحتی میتواند امواجی با شدتهای بالاتر از ۸۵ دسی بل را سد کند. از این ویژگی منیزیم برای تولید بدنه تلفنهای همراه، تجهیزات الکترونیکی، نظامی و تولید سیمهای انتقال اطلاعات پرتوان استفاده میشود.
یکی دیگر از خصوصیات آلیاژهای منیزیم در مقایسه با آلومینیوم پایداری ابعادی در برابر تغییرات حرارتی میباشد. در منیزیم، پارامترهای مختلف خواص حرارتی مانند رسانایی پایینتر و گرمای ویژه بالاتر از آلومینیوم میباشد. از جمله فرایندهای تحت تأثیر خواص حرارتی ماشین کاری دقیق میباشد. آلیاژهای منیزیم حین گرم و سرد شدن سریع در فرایند ماشین کاری، تغییرات ابعادی کمی دارند. این ویژگی ماشین کاری دقیق این آلیاژها را سادهتر میسازد.
منیزیم در مقایسه با آلومینیوم، سیالیت بالا در ریختهگری، نیاز به فشار کمتر در دایکست و عدم واکنش با فولاد در بوته و قالب میباشد. با در نظر گرفتن این مزایا میتوان برای دایکست قطعهای منیزیمی از دستگاههای دایکست با ظرفیت کمتر استفاده نموده و تعداد به مراتب بیشتری قطعه در قالبهای مشابه فولادی تولید کرد.
تولید منیزیم از آب دریا
در روش تولید منیزیم از آب دریا، منیزیم به صورت هیدروکسید رسوب کرده و بوسیله واکنش با اسید کلریدریک، به کلرید منیزیم تبدیل میشود. کلرید منیزیم بوسیله تبخیر محلول، بازیافت شده و فلز منیزیم بوسیله الکترولیز نمک مذاب بدست میآید.
فرایند الکترولیت
اولین مرحله از این فرایند فراهم کردن کلرید منیزیم-که بطور جزئی دهیدراته شده- یا کارنالیت دهیدراته میباشد. تغذیههای سلول صنعتی شامل مخلوطی از کلرید منیزیم دهیدراته، کلرید منیزیم جزئی دهیدراته شده یا کارنالیت دهیدراته میباشد.
کلرید منیزیم دهیدراته شده بوسیله یکی از این دو روش فراهم میشود: کلریده کردن اکسید منیزیم یا دهیدراته کردن آب نمک کلرید منیزیم.
سلول الکترولیتی شامل مخزن آجر کاری شدهاست که به محفظههای کاتد و آند تقسیم میشود. آند گرافیتی هوا- خنک شونده یا آب- خنک شونده و کاتد فولادی در الکترولیت متشکل از کلریدهای قلیایی با افزودنی کلرید منیزیم، غوطه ور میشوند. دمای کاری بین ۷۵۰–۶۸۰ درجه سانتی گراد است. کلرید منیزیم در سلول الکترولیتی مطابق واکنش زیر تجزیه میشود:[۳]
MgCl_2→Mg+Cl_2
منیزیم فلزی در کاتد تشکیل شده (روشنتر از الکترولیت است) و شناور میشود تا در قسمت کاتد جمع شود. کلر که محصول فرعی این فرایند است در آند جمع میشود.
در کشورهایی که انرژی الکتریکی ارزان است و بازار مصرف پایداری وجود دارد، تولید به روش الکترولیز به صرفه است. این مقرون به صرفه بودن زمانی بیشتر است که کلرید منیزیم مورد نیاز از منبعی مثل آب دریا تأمین شود.[۴]
فرایند احیای سیلیکوترمی
منیزیم طی فرایند سیلیکوترمی در دماهای بالا با فروسیلیسیم کاهش یافته و کریستالهای منیزیم تشکیل میشوند. این فرایند شامل احیای اکسید منیزیم مذاب بوسیله فروسیلیسیم تحت فشار گاز در دمای حدود ۱۴۰۰ درجه سانتی گراد میباشد. منیزیم فلزی در این فرایند تشکیل شده، تبخیر میشود و سپس دور از منطقه گرم تقطیر میگردد. منیزیم تقطیر شده دارای خلوص ۹۹٫۸٪ است و سپس مجدداً ذوب و ریختهگری میشود.[۵]
حال در انتهای این بخش به دلیل موضوعیت این فرایند در گزارش تهیه شده و استفاده از این روش به عنوان تنها روش تولید منیزیم در کشور، لازم دیده میشود که این فرایند را بهطور خلاصه شرح دهیم.
به صورت کلی این فرایند از ۴مرحله اصلی و چندین مرحله کنترلی تشکیل شدهاست که در ادامه به آنها پرداخته میشود.
واحد کلسیناسیون
در ابتدای این بخش سنگهای دولومیت استخراج شده پس از دپوسازی به واحد کنترل منتقل شده و میزان خلوص منیزیم در آن مورد بررسی قرار میگیرید، پس از تأیید شدن سنگهای استخراجی، این سنگها را غربال کرده و از لحاظ ابعادی بهینه میگردند. سپس به منظور افزایش خلوص منیزیم موجود در دولومیتهای استخراجی و آمادهسازی برای تحویل به بخش احیا، سنگها را وارد کورهٔ دوار میکنند، در این بخش سنگهای موجود در دمای ۱۲۰۰درجه سلسیوس قرار گرفته و گاز دیاکسید کربن خود را همانطور که در معادله زیر به آن اشاره شدهاست از دست میدهند.
(MgCO_3.CaCO_3 (solid)+Q→MgO.CaO(solid)+2CO_2+O_2(g
پس از گذر سنگهای مورد نظر از این بخش، سنگهای خاکستری اولیه به رنگ سفید درآمده و به بخش بعدی منتقل میگردد. لازم است ذکر شود که گاز خروجی از این کوره حاوی مقادیر قابل توجهی از آب و دیاکسید کربن میباشد که بررسی چگونگی استفاده از ضایعات تولیدی خود میتواند مفصلاً مورد بررسی قرار گیرد.
واحدآسیا و بریکت سازی
در این بخش دولومیتهای کلسینه شده به منظور آمادهسازی برای تحویل به بخش احیا به نسبتهای مشخصی با فروسیلیس(۷۵درصدکربن) و فلورین مخلوط میگردد، این مواد مخلوط شده سپس وارد آسیا گشته و در چندین مرحله پودر میشوند.
پس از مراحل فوق موادآسیا شده به منظور بهینهسازی شکلی و ابعادی، به شکل بریکت درآورده شده و در محفظههایی برای انتقال به مرحله بعد نگهداری میشوند.
ریتورت واحد احیاء منیزیم
واحد احیاء منیزیم
در این مرحله بریکتها را درون محفظهای استوانهای شکل که ریتورت نام دارد، شارژ میکنند. پس شارژ ریتورتها، داخل محفظه ریتورتها توسط دو پمپ خلأ در دو مرحله تخلیه میشود، اولین پمپ فشار داخل ریتورت را به فشاری در حدود ۱۱۰ پاسکال رسانده و پمپ دیگر این فشار را به حدود ۱۰الی ۵ پاسکال میرساند. ابن فرایند احیاء حدود ۱۰ ساعت به طول میانجامد که در طی آن منیزیم موجود در بریکتها توسط فروسیلیس احیاء شده و به سمت دیگر ریتورت که کندانسور تعبیه شده و فشار کمتری دارد منتقل میشود. سپس منیزیم در محفظهٔ ابتدایی ریتورت که محفظه چگالش نام دارد از گاز به جامد تبدیل میشود که به اصطلاح آن را کرون یا تاج منیزیم مینامند. بقیه مواد داخل ریتورت که بریکت سوخته نام دارند نیز از ریتورتها تخلیه و در به عنوان دور ریخت جمعآوری میشود. فرایند گفته شده در بالا در معادله زیر خلاصه میشود.
کرونهای تولید شده در واحد احیاء
(2MgO.CaO(s)+Si(Fe)(s) →2Mg(g) +CaO.SiO_2(s) +Fe(s
واحد ریختهگری
کرونهای تولید شده در مرحله قبل، به خلوص مورد نظر رسیدهاند ولی به دلیل اشکال و اندازه غیر استاندارد و بد کرونهای سرد شده نیاز است که این کرونها در کورهها دوباره ذوب شده و برای بستهبندی و فروش به شمش تبدیل شوند.
تولید منیزیم در ایران منحصر به کارخانه منیزیم فردوس می شود که با ظرفیت اسمی 6 هزار تن در سال و از دلومیت به روش احیای سیلیکوترمی صورت می گیرد.
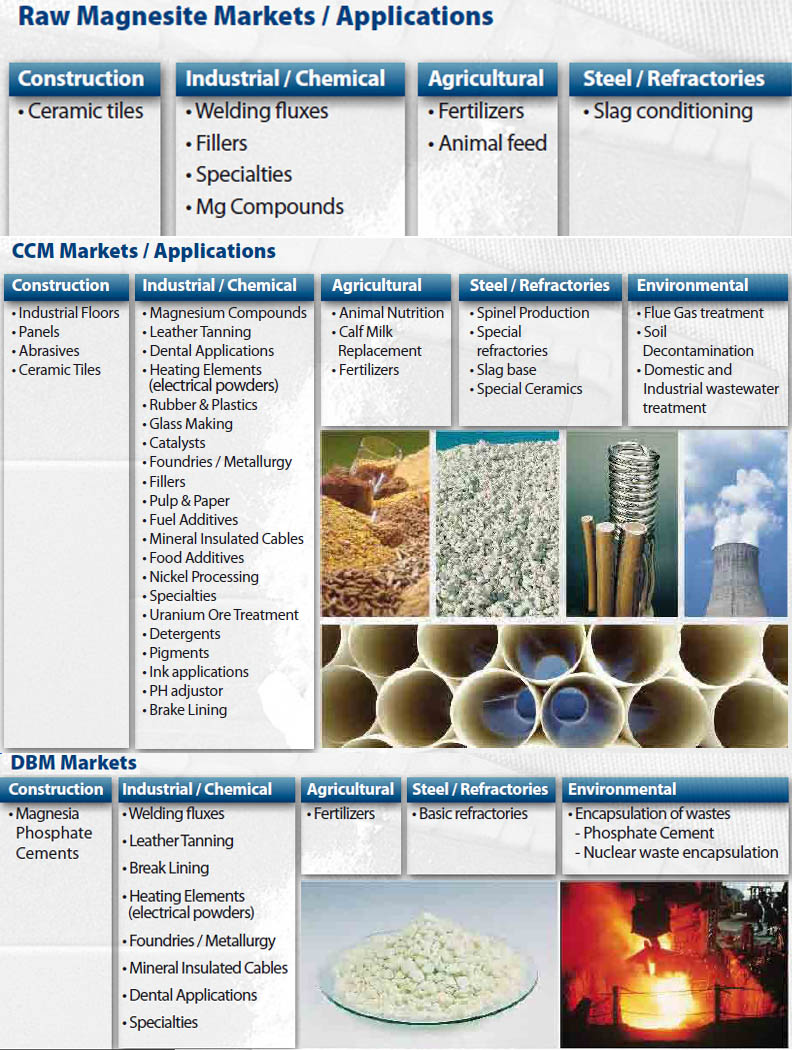
تولید-شمش-منیزیم - منیزیت کانیای است که نقش اصلی را در صنایع دیرگداز و نسوز دارد. فرآوردههای منیزیتی، به طور عمده شامل دیرگدازها میباشند که در بخش صنایع دیرگداز به فراوانی استفاده میشود. بخش دیگری از این فرآورده ها، در مصارف کشاورزی، داروسازی، شیمی و ... بهکار برده میشود. امروزه فولادسازی مدرن و درحال توسعه، نیاز به افزایش تولید دیرگدازهای منیزیتی با کیفیت بالا دارد. منیزیت کاملا تکلیس شده، شامل بلورهای پریکلاز در یک زمینهی بلورین دانه ریز میباشد و نقطهی ذوب آن، 2800 درجه سانتیگراد و وزن مخصوص آن 6/3 گرم بر سانتیمترمکعب است. برای افزایش مقاومت گرمایی و پایداری فرآوردههای منیزیتی، 5 تا 12 درصد آلومین افزوده میشود که این عمل منجر به تشکیل یک فاز اسپنیلی از MgO میگردد. ذخیره و تولید جهانی منیزیت: ذخایر قطعی منیزیت دنیا، 5/2 و ذخایر پایهای آن 4/3 میلیارد تن میباشد. تولید سالانه منیزیت در سطح دنیا در حدود 20 میلیون تن است که از این مقدار، بیشترین سهم مربوط به کشورهای تازه استقلال یافتهی شوروی، چین، کره شمالی، چک و اسلواکی بوده است. کشورهای اصلی تولیدکننده استرالیا، یونان، ترکیه، اسپانیا، برزیل، یوگوسلاوی، هند و کانادا هستند.
بیشتر بخوانید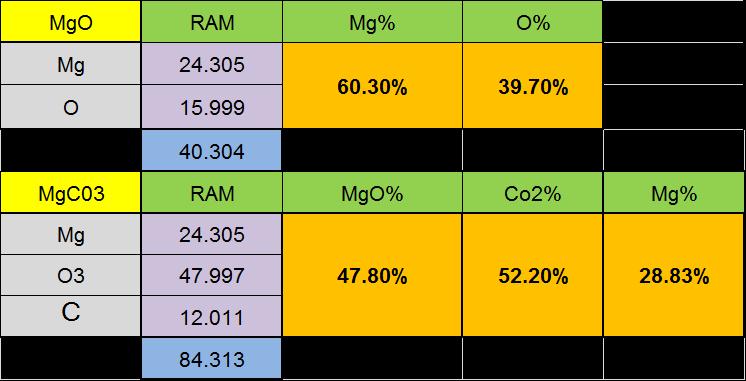
تولید-شمش-منیزیم - از آنجا که بعد از انجام آنالیز در آزمایشگاه، مقداری LOI گزارش می شود، لازم است برای محاسبه عیار واقعی در نمونه محاسبات زیر انجام شود. لذا همیشه در انجام آنالیز، باید مقدار LOI محاسبه گردد. فرض کنید پس از ارسال یک نمونه اکسید منیزیم کلسینه از محصولات شرکت پرشیا پایا معدن به آزمایشگاه نتایج و مقادیر زیر گزارش شده باشد: MgO: 85.19 SiO2: 8.12 Al2O3: 0.17 CaO: 2.41 Fe2O3: 1.4 LOI: 2.8 با توجه به آنالیز فوق مقدار 85.19% از وزن کل بار خریداری شده مربوط به اکسید منیزیم میباشد. اما آنچه برای مصرف کننده مهم میباشد خلوص محموله خریداری شده است، برای این منظور میبایست درصد وزنی MgO را برای حالتی محاسبه کرد که تمام LOI از نمونه حذف شده باشد: 100-2.8= 97.2 (85.19/97.2)*100=87.64 درصد مثالی برای کربنات منیزیم: MgO: 42.91 SiO2: 6.13 Al2O3: 0.33 CaO: 2.14 Fe2O3: 1.2 LOI: 46.85 100-46.85= 53.15 (42.91/53.15)*100= 80.73 درصد
بیشتر بخوانید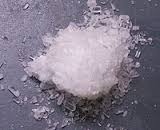
تولید-شمش-منیزیم - سولفات منیزیم ازسولفات منیزیم به عنوان کود شیمیایی در خاک هایی که کمبود منیزیم دارند استفاده میشود. منیزیم تنها عنصر فلزی موجود درکلروفیل می باشد و به عنوان هسته مرکزی سازنده کلروفیل معرفی میشود. بنابراین منیزیم بطور غیر مستقیم در متابولیسم و فتوسنتز درختان میوه نقش دارد. منیزیم همچنین در فعالیت آنزیم ها در گیاهان نقش داشته و حامل های فسفری را که در جذب سایر عناصر موثر میباشند فعال می کند. منیزیم با شرکت در چرخه اسید سیتریک بهعنوان یک چرخه متابولیسمی در گیاه، در تنفس گیاهان دخالت دارد. منیزیم در درختانیکه تولیدروغن میکنند مانند زیتون، نقش مثبتی در افزایش روغن تولیدی دارد، این موضوع در مورد گردو و بادام نیز صادق است. این عنصر در سنتز پروتئین در گیاهان نیزدخالت دارد. در درختان میوه هسته دار مانند هلو، گوجه سبز و مرکبات، منیزیم درساخت هسته نقش فعالی دارد. اين عنصر بصورت كاتیون دو ظرفیتي Mg+2 توسط گیاهجذب میشود. شكل تجاري اين عنصر بصورت دولومیت، سولفات منیزيم با ۱۴و ۱۶% منیزیم واكسید منیزيم با ۳۶% منیزيم دردسترس میباشد.
بیشتر بخوانید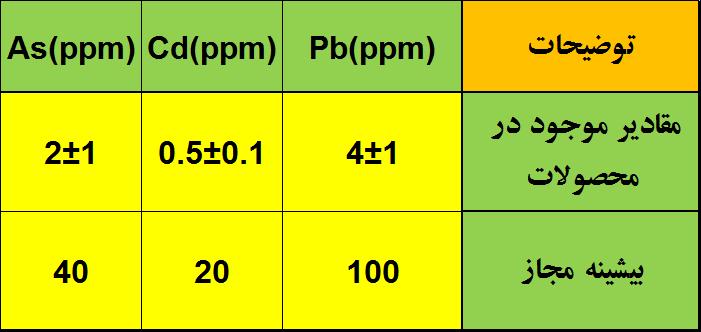
تولید-شمش-منیزیم - با توجه به شرایط خاص تعریف محصولات منیزیتی برای بازار خوراک دام و طیور پس از رایزنی های بخش فنی و بازرگانی جدول پیوست برای این بازار طراحی گردید. با توجه به مقادیر پایین فلزات سنگین در محصولات (جدول پیوست)، مفتخریم بتوانیم نیاز بازار خوراک دام وطیور و مجموعه های مکمل سازی را با استاندارد بالا و یکنواختی در تولید، تامین نماییم.
بیشتر بخوانید
تولید-شمش-منیزیم - همانطور که در تصاویر مشاهده میشود، پس از استخراج، خردایش و فراوری منیزیت تولید شده به ترتیب عیار و سایزهای مختلف در مکانهای مشخص و آماده سازی شده به صورت جداگانه دپو میشود و پس از نهایی شدن سفارش و برنامه تولید با نظارت کارشناس مربوطه در معدن بارگیری میشود.
بیشتر بخوانیدتولید-شمش-منیزیم - با توجه به تعریف مصارف مختلف برای فورستریت در صنایع دیرگداز و فولاد و همچنین امکان تولید این کانی در معادن شرکت پرشیا پایا معدن، جدول آنالیز این محصول به پیوست ارایه میگردد. بخش فنی این شرکت جهت مذاکرات فنی و تعریف فاز پایلوت و تست های اولیه برای امکان سنجی در صنایع مذکور، اعلام آمادگی مینماید.
بیشتر بخوانید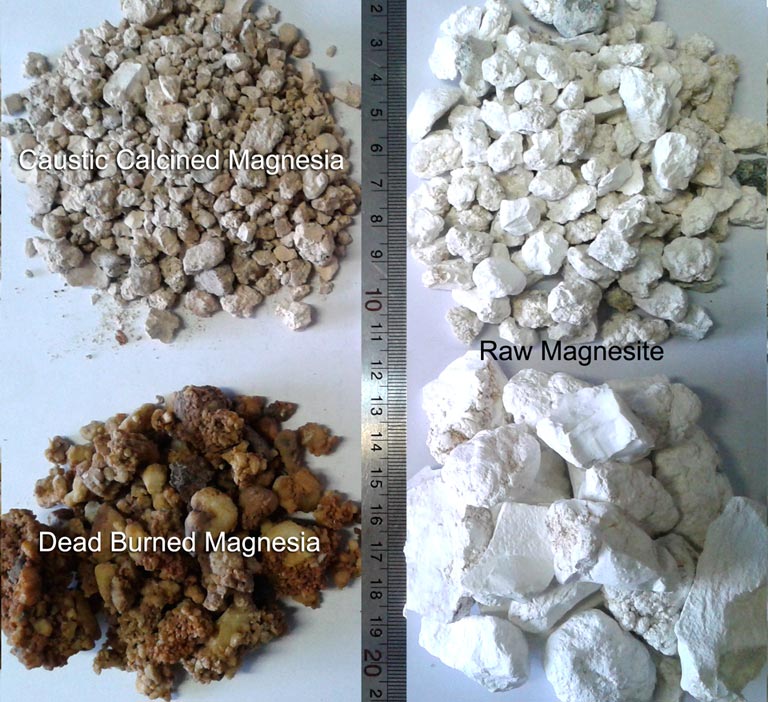
تولید-شمش-منیزیم - به عنوان كود: حداقل 80% MgO، پودر مش 200 خوراک دام وطیور: حداقل 65% MgO، (پودر مش 150) سیمان منیزیتی(سُرِل): آهك و آهن كم (معمولا كمتر از 3) در تهيه لقمه هاي ساب سنگ و توليد سيمان حفاري و توليد بوردهاي منيزيم(پودر مش 350) داروسازی: MgO > 98%، در هیدروكسید منیزیمMgO>95% ، سفید، غیر محلول در آب و خاصیت بازی قابل واكنش با فنلفتالئین، Fe 0.05%، آرسنیك 3 ppm ، فلزات سنگین40 ppm ،
بیشتر بخوانید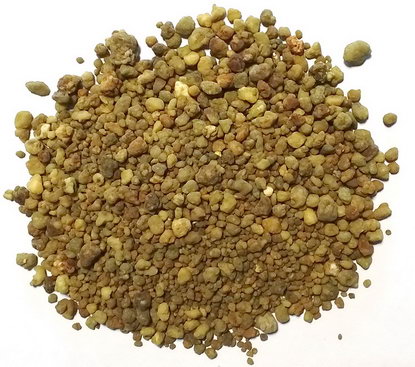
تولید-شمش-منیزیم - نسوز درجه یك: حداقل MgO 99-96% ، Fe2O3<0.2، نسبت SiO2:CaO، 1:3 یا 1:4 ، دانسیته 44/3، B2O3<0.01 نسوز درجه دو: MgO:94-95 ، CaO:1-3%، Fe2O3:0.5-0.8%، Al2O3:0.2-0.8%، SiO2:0.5-3.5%، دانسیته كمتر از 3.5 و بلورهای درشتدانه بيش از 50 ميكرون. نسوز درجه سه: MgO:86-92 ، CaO:1-8%، Fe2O3:0.5-3%، Al2O3:0.2-1.5%، SiO2:3-10%، دانسیته كمتر از 3.3 و بلورهای پريكلاز بيش از 30 ميكرون.
بیشتر بخوانید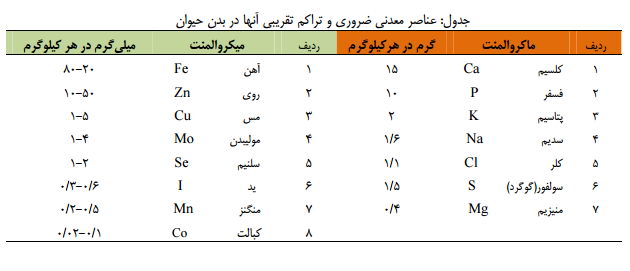
تولید-شمش-منیزیم - منيزيم رابطه بسيار نزديكي با عناصر كلسيم و فسفر دارد. تقريباً 70% كل منيزيم در استخوانها و مابقي در بافتهاي نرم و مايعات بدن پراكنده است. منيزيم به وسيلة غذاهاي مختلف وارد بدن دام وطيور ميگردد، در دانة غلات نيز قسمتي از منيزيوم به صورت تركيب با اسيدفيتيك ميباشد سبوس گندم، مخمر خشك، و مكملهاي پروتئيني گياهي بخصوص كنجالة پنبه و كنجالة كتان از منابع خوب منيزيم ميباشند وظايف: منيزيم معموليترين فعالكنندة آنزيم بوده و در فعال نمودن فسفات ترانسفرازها، ديكربوكسيلازها، و اسيل ترانسفرازها اهميت دارد. براي رشد اسكلت به عنوان جز تشكيل دهنده استخوان ضروري است. براي انجام واكنشهاي فسفريلاسيون اكسيداتيو در ميتوكندري قلب و ساير اعضا ضرورت دارد. كمبود در اثر كمبود منيزيم در گوسفندان و گاوهاي شيرده بيماري بروز ميكند كه آن را تتانيگراس= كزاز علفي، ( تتانيشيردهي) و (تتاني هيپوماگنزامي) مينامند. حيوان مبتلا داراي علائمي همچون بي اشتهائي، عصبي، چشم- هاي خيره، انقباض و گرفتگي عضلات و پاهايي ضعيف و كج ميباشند. چنانچه گرفتگي عضلات معالجه نگردد، درصد مرگ ومير بالا ميرود. گرفتگي عضلات سبب زمين گير شدن دام مي گردد. در اثر كمبود منيزيم فعاليت چند آنزيم آلكالين فسفاتاز پلاسما، انولاز و پيرووات فسفوكيناز عضله كاهش مي يابد و لذا حيوان دچار گرفتگي عضلاني مي شود. كمبود منيزيم در طيور باعث بروز اغماء و تشنجات عصبي گرديده، در جوجهها موجب نرمي و پيچخوردگي استخوانها ميشود. رشد مرغهاي گوشتي كم شده ميزان توليد در مرغهاي تخمگذار كاهش مييابد. به علاوه مواد آهكي پوسته تخممرغ كم ميشود و در نتيجه پوسته تخممرغ نرم و به اشكال غيرطبيعي (دفرمه شدن پوسته تخم مرغ) در ميآيد. كزاز علفي اختلال متداول گاو و گوسفندان در حال چرا به دليل كمبود منيزيم را كزاز علفي گويند. اين اختلال كزاز منيزيمي و يا مسموميت با مرتع گندم نيز شناخته مي شود. - در دامهاي با جيره خشك زمستانه با تداوم مصرف بالا نيز اتفاق مي افتد. - استفاده زياد از غلاتي مانند گندم به دليل جذب سريع پتاسيم نيز از عوامل بروز كزاز علفي است. مقادير بالاي پتاسيم و پروتئين جيره نيز سبب بروز چنين اختلالي مي گردد. - افزودن چربي نيز به دليل اينكه تشكيل صابون منيزيم (كمپلكس منيزيم) و به سادگي جذب نميگردد، سبب كاهش جذب منيزيم و در نهايت كزاز علفي مي شود. زيادي منيزيم مسموميت ايجاد مي كند. منابع منيزيم جهت افزودن به جيره دام 1- اكسيد منيزيم (2 (MgO - كربنات منيزيم و 3- سولفات منيزيم تزريق محلول تزريقيCMP در حالت اورژانسي، دام زمين گير را بهبود بخشيده ولي استفاده از مكمل معدني بهترين عامل از بروز مجدد آن است.
بیشتر بخوانید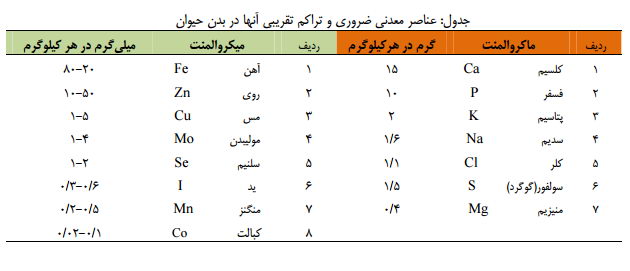
تولید-شمش-منیزیم - علاوه بر سه گروه مواد مغذي كربوهيدراتها، چربيها و پروتئينها مواد معدني (مينرالها) در تغذيه موجودات زنده گياهي و حيواني اهميت قابل ملاحظهاي دارند. وجود عناصر معدني به ميزان مورد نياز و كافي به جهت «توليد محصولات » دام و طيور ضروري است. به طور كلي 2 -5% وزن بدن دام و طيور را عناصر معدني «خاكستر» 2 مختلف، رشد و نگهداري Ash تشكيل ميدهد كه از اين ميزان تركيبات معدني، در حدود 85% آنها به صورت ذخيره در اسكلت وجود دارد. نقش فيزيولوژيكي و اساسي عناصر معدني بسيار گوناگون و مهم بوده و شناسايي نقش آنها جهت پرورش دام و طيور و تنظيم برنامه هاي غذائي داراي اهميت بسيار بالائي است. به همين خاطر در جيره نويسي براي دام وطيور معمولا 1 تا 2 درصد مواد معدني اضافه ميكنند. زمینه های مختلف تاثیر مواد معدنی عبارتند از : 1) نقش انرژيزائي 2) نقش فيزيكو شيميائي: 2-1 كنترل تحريك پذيري اعصاب و عضلات (سديم، پتاسيم، كلسيم، منيزيم) Na/K/Ca/Mg 3) نقش سازندگي 3-1شركت در ساختمان بافت استخواني و تشكيل اسكلت بدن دام (Mg , P , Ca). 4) نقش عملي مواد معدني بر حسب ميليگرم mg در هر كيلوگرم مادة بدن به دو دسته عناصر 1) ماكرو 2 Macro- ميكرو Micro تقسيمبندي شدهاند. ـ عناصري همچون كلسيم، فسفر، منيزيم، سديم، پتاسيم، كلر و گوگرد كه مقدار متوسط آنها به ازاء هر كيلوگرم مادة بدن به 50 ميليگرم بالغ ميشود را مواد معدني پرمصرف يا ماكروالمنت گويند.
بیشتر بخوانید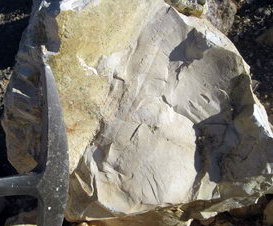
تولید-شمش-منیزیم - منیزیت با فرمول MgCO3 به عنوان مهمترین و باارزشترین کانی منیزیم شناخته میشود. این کانی به عنوان عضوی از گروه کربناتها در سیستم تریگونال، رده اسکالنوئدریک متبلور میشود. به ندرت به صورت فرم بلوری دیده میشود و در صورت تشکیل به شکل رومبوئدری میباشد.عموما همراه کانیهای هونتیت، هیدرومنیزیت و کرومیت مشاهده میشود. در ترکیب شیمیایی آن 47.8 درصد اکسید منیزیم و 52.2 درصد دیاکسید کربن وجود دارد. ممکن است مقداری آهن جانشین منیزیم شود، که در صورت افزایش آهن، ترکیب شیمیایی آن به سمت سیدریت پیش میرود. همچنین ممکن است مقداری کلسیم و منگنز نیز در ترکیب آن دیده شود. ساختار آن مشابه با کلسیت است. کانی منیزیت دارای رنگ سفید، خاکستری، زرد با رنگ خاکه سفید و جلای شیشهای تا مات بوده و وزن مخصوص آن 9/2 تا 1/3 گرم بر سانتیمتر مکعب با سختی 5/3 تا 5/4 در مقیاس موهس میباشد. از مشخصات ظاهری آن شکست صدفی و رخ رمبوئدر است. با جلای شیشهای شفاف تا نیمه شفاف ظاهر میشود.
بیشتر بخوانیدتولید-شمش-منیزیم - با توجه به مقادیر پایین فلزات سنگین در محصولات (تصویر پیوست)، مفتخریم بتوانیم نیاز بازار خوراک دام وطیور و مجموعه های مکمل سازی را با استاندارد بالا و یکنواختی در تولید، تامین نماییم.
بیشتر بخوانید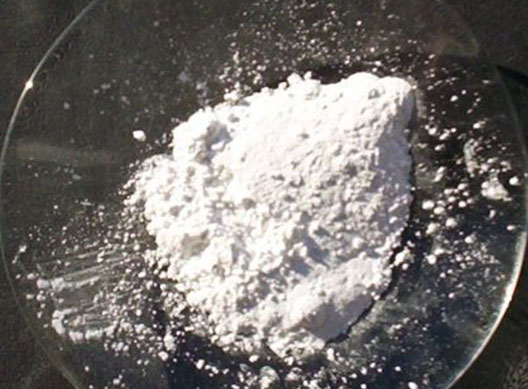
تولید-شمش-منیزیم - اکسید منیزیم چیست ؟ اکسید منیزیم با فرمول شیمیایی MgO ماده ای جاذب رطوبت و سفید رنگ بوده و بعنوان یک منبع منیزیم شناخته میشود. اکسید منیزیم از طریق کلسینه سازی کربنات منیزیم یا هیدروکسید منیزیم و یا فراوری کلرید منیزیم بوسیله آهک و حرارت تولید میشود. از اکسید منیزیم بطور گسترده ای در صنعت فرآورده های نسوز، اصلاح آبهای زیر زمینی، تصفیه هرزآبها، تصفیه آبهای آشامیدنی و …. استفاده میشود. بعلاوه، خاصیت بافری اکسید منیزیم در محیطهای اسیدی و قابلیت آن در تثبیت فلزات سنگین نامحلول، از جمله دلایل کاربرد گسترده این ترکیب در صنایع مختلف میباشد. در سال ۲۰۰۴ حدود ۷۵ % از اکسید منیزیم تولید شده در امریکا در صنعت تولید مواد نسوز استفاده شد و ۲۵% باقی مانده در صنایعی همچون کشاورزی، شیمیایی، ساختمان سازی و سایر صنایع استفاده شد.
بیشتر بخوانیدتولید-شمش-منیزیم - یکی از موارد مصرف منیزیت و یا کربنات منیزیم تولید شده در این شرکت، در صنعت کاشی و سرامیک میباشد. که کارخانجات محترم کاشی و سرامیک پس از انتخاب آنالیز مورد نیاز از محصولات شرکت و ساخت انگوب، از این محصول برای جلوگیری از چسبیدن ذرات مواد بدنه کاشی به رولرهای سرامیکی در منطقهfiring کوره استفاده میکنند.
بیشتر بخوانید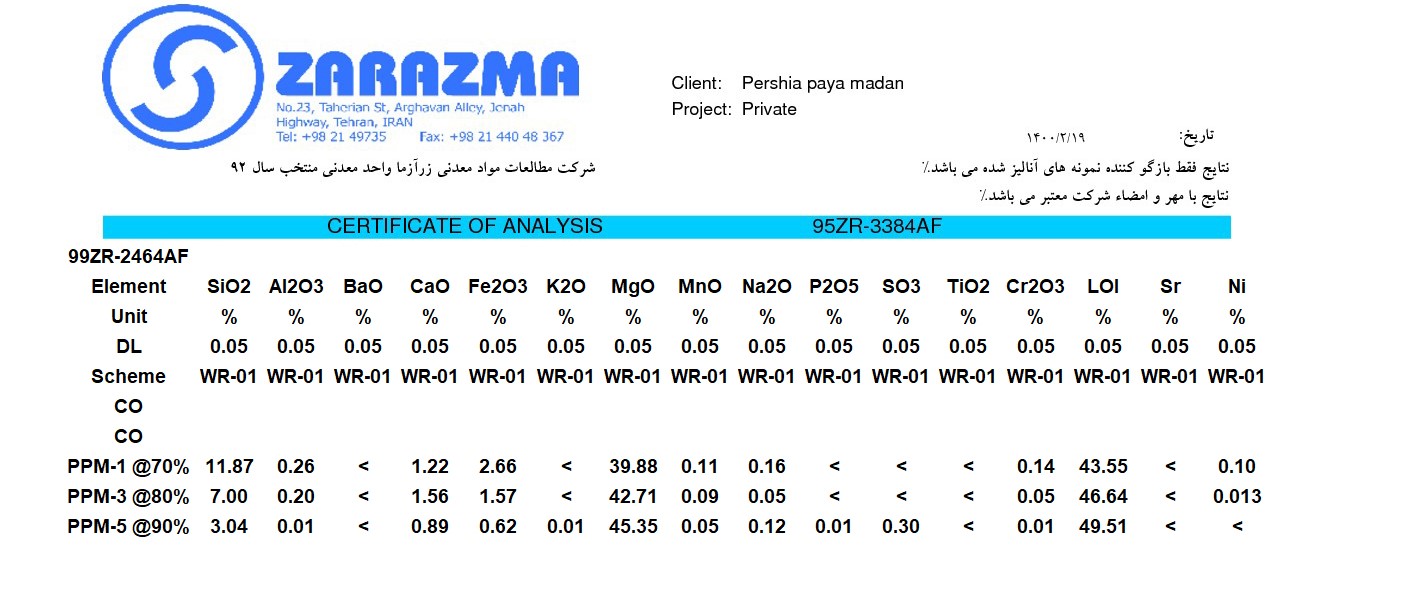
تولید-شمش-منیزیم - آنالیز XRF از محصولات شرکت پرشیاپایا معدن.
بیشتر بخوانیدتولید-شمش-منیزیم - بخش عمدهای از ذخایر منیزیت از تجزیه سنگهای آذرین اولترابازیک مانند پریدوتیت و دونیت بهوجود میآید. همچنین منیزیت در رگهها و تودههای نامنظم هیدروترمال در سنگهای آهکی دولومیتی یافت میشود. همچنین از تجزیه سنگهای دگرگونی غنی از کانیهای منیزیمدار تولید میشود. ذخایر منیزیت، به شکلهای متفاوتی به وجود می آیند. الف) منیزیت گرمابی پیدایش این گونه ذخایر، نتیجه دگرسانی محلولهای گرمابی حامل CO2 بر روی سنگهای اولترابازیک است. ذخایر منیزیت تشکیلشده در این فرآیندها، معمولاً به صورت توده ای و نهان بلورین هستند و اغلب دارای عیار بالای 90% می باشند. ب) منیزیت جانشینی گرمابی این ذخایر از محلولهای گرمابی که از ژرفای زمین سرچشمه میگیرند، تشکیل میشوند. این محلولها در هنگام مهاجرت بر سطح و در برخورد با سنگهای آهکی، سنگهای دولومیتی، یا شیل، بر اثر متاسوماتیسم جانشینی، ذخایر منیزیتی متبلور را به وجود میآورند. این گونه ذخایر در ایران مورد توجه قرار نگرفته است، هر چند امید به تشکیل این ذخایر در خاور ایران، شمال باختری ایران (آذربایجان باختری) و نقاط دیگر میرود. پ) منیزیت تراوشی در این نوع، CO2 موجود در آب های جوی بر روی سنگهای سرپانتینی و اولترامافیکی اثر می کند و سبب واکنش های شیمیایی و تشکیل منیزیت می شود. ذخایر منیزیتی از این نوع، اغلب کوچک و به صورت رگچهای می باشند. در ایران، در ناحیه افیولیت های نایین (سهیل باکوه) و سبزوار این گونه ها دیده می شود. ت)منیزیت رسوبی این گونه ذخایر در محیطهای رسوبی نزدیک به سنگهای غنی از منیزیم و به صورت تودهای و نهان بلورین (یا به صورت تراورتن) تشکیل میشوند. این گونه ذخایر در پاره ای موارد می تواند از لحاظ اقتصادی قابل بهره برداری باشند. اما اغلب کم عیار هستند. پیدایش ذخایر توده ای منیزیت در محیط های آب شیرین، نیازمند فراهم بودن یون منیزیم است. یون های منیزیم حاصل از تخریب شیمیایی سنگهای غنی از منیزیم، به محیط های دریاچه ای یا آبگیرهای فصلی آورده شده و سرانجام ذخایر منیزیتی را پدید می آورند. در بسیاری از نقاط ایران، همه شرایط یاد شده موجود است، ولی برای اکتشاف منیزیت های رسوبی تاکنون فکری نشده است. ذخایر منیزیت ایران از کرتاسه پسین تا کواترنر تشکیل شدهاند.در این فاصله زمانی، باتوجه به شرایط منیزیت، دوره به خصوصی را نمی توان برای تشکیل آن مشخص کرد.
بیشتر بخوانید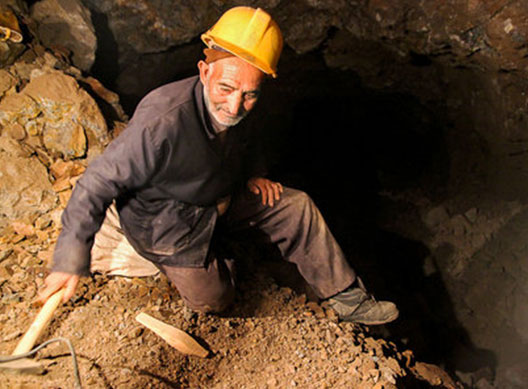
تولید-شمش-منیزیم - اثر ترکیب شیمیایی سرباره مصنوعی جهت جلوگیری از خوردگی نسوز منیزیت- کربنی آجر نسوز منیزیت- کربنی به علت ویژگی های خاص در دیرگدازی و عدم ترشوندگی با مذاب فولاد، در صنایع فولاد سازی توجه زیادی را به خود جلب کرده است. نسوز منیزیت کربنی در کنار مزایای خوب خود باعث خوردگی باغ با سرباره و کاهش عمر نسوز می شود. در این تحقیق، اثر افزودنی های متفاوت به سرباره کوره پاتیلی جهت جلوگیری با به حداقل رساندن خوردگی نسوز منیزیت کربنی مورد توجه قرار گرفته است. نتایج نشان می دهد که از آمیختن موادی چون ماده معدنی دولومیت پخته شده، پودر آجر منیزیت کربنی فرسوده(ضایعات)، اکسید منیزیم زینتر شده به نسبت های مختلف 15% و 30% از هر کدام با سرباره عمر نسوز افزایش می یابد و بهترین نتایج کاهش خوردگی و افزایش مقاومت در برابر سرباره از افزودن ماده معدنی دولومیت حاصل می گردد.
بیشتر بخوانید
تولید-شمش-منیزیم - در مقاله ی حاضر به بحث بیماری کمبود منیزیم (هیپومنیزی )تتانی می پردازیم : بیماری های متابولیکی بدن گاو دارای ذخایری از منیزیم است که قسمت عمده آن در استخواﻧﻬای دنده و مهره ها نگهداری میشود. در مواقعی که در دامهای جوان، کمبود منیزیم اتفاق می افتد، به میزان زیادی می توانند از ذخیره منیزیم استخواﻧﻬایشان استفاده کنند. ولی دامهای بالغ به علت عدم توانایی از ذخایر منیزیمی در اثر بروزTetany تلف می شوند. بنابراین تامین منیزیم از طریق جیره غذایی در نشخوار کنندگان امری حیاتی است. منیزیم از طریق ادرار، مدفوع و شیر دفع می شود و تنظیم بین منیزیم سرم خون (بدن ) و منیزیم را که حیوان روزانه از دست می دهد از طریق جذب منیزیم از دستگاه کوارش صورت می گیرد. بنابراین تامین منیزیم در جیره غذای نشخوارکنندگان ضروری است. در گوساله ها تاسن 1 ماهگی، منیزیم هم از روده کوچک و هم از روده بزرگ جذب (انتشار ساده ) می شود . با افزایش سن دام و فعال ش دن شکمبه، منیزیم از طریق شکمبه (انتقال فعال) جذب میشود. علت متداول بودن کمبود منیزیم در دامهای مسن تر، متراکم بودن ساختمان استخوان آﻧﻬا می باشد . ولی در گاوهای جوان شبکه استخوانی باز است و ذخیره منیزیم به سهولت در دسترس میباشد. هیپومنیزیمی در گوساله هایی که عمدتاً از شیر مادر تغذیه می آنند و غالباً مکمل به آﻧﻬا داده نمی شود بیشتر از گوساله های همسنی هستند که علاوه بر شیر از غذای مکمل هم استفاده می کنند. زیرا میزان منیزیم شیر بسیار ناچیز است. عوامل مستعد کننده کمبود منیزیم: - 1) داروهایی که باعث افزایش ادرار می شود مثل( فروزماید) -2) وقتی دام دچار اسهال های مداوم شود . مانع از توقف مواد غذایی در دستگاه گوارش و میشود) mg جذب -3) دامهای پرشیر بیشتر در معرض کاهش منیزیم خون قرار دارند. -4) گرسنگی دام بمدت 24 48 ساعت، باعث کاهش عیار منیزیم میشود. -5) افزایش پروتئین جیره به علت اینکه در شکمبه تولید آمونیاک زیادی می کند و باعث کمبود منیزیم میشود. -6) استفاده از کودهای آمونیوم بمیران زیاد باعث تولید آمونیاک درشکمبه شده و جذب منیزیم را کاهش میدهند. -7) وجود پتاسیم زیاد مانع از جذب منیزیم گیاه میشود. -8) فعالیت غده تیروئید (هیپرتیروئید) باعث کاهش منیزیم سرم میشود. در اوایل وجود دارد، فعالیت N.E.B شیرواری در گاو که تیروئید افزایش مییابد. -9) جایگاه های بدون سرپناه در هوای سرد و مرطوب و طوفانی از عوامل مهم در کمبود منیزیم میباشند. این عامل به دلیل دفع زیاد ادرار و مصرف نکردن غذا و آزاد شدن هورمون استرس (آدرنالین) باعث کاهش منیزیم میشود. -10 )افزایش آلمینیوم جیره مانع از جذب منیزیم میشود. (Hypo magnesium Tetany) کزاز شیرواری اسامی دیگر این بیمیاری عبارت است از: (Grass Tetany) کزاز علفی ، (Lactation Tetany کزاز شیرواری (Wheat Pasture Poisoning) و مسمومیت مرتع گندم (Grass Staggers) گیجی علفی این بیماری خاص نشخوارگنندگان است . (اکثر در گاوهای شیری دیده میشود) علت بروز این بیماری کاهش منیزیم سرم است و در صورت عدم درمان بموقع بیماری کشنده است و مرگ بر اثر اختلالات تنفسی اتفاق میافتد. این بیماری در گاوهای شیری بیشتر در سنین 4 7 سالگی و در دوماه پس از زایش بیشتر دیده می شود. ولی بیماری می تواند در گاوهای گوشتی، گوساله ها، تلیسه ها و گاوهای خشک هم دیده شود. میزان منیزیم سرم در نشخوار کنندگان dlit1/ 3 7 mg dlit1 می – mg است. در بیما ران کمبود منیزیم مزان آن به رسد. پاتوژنز: کاهش منیزیم سرم، آزاد شدن استیل کولین را تسهیل میکند و منجر به بروز تتانی می شود . البته میزان کاهش نشان می دهد و شاید دلیل وجود علائم C.S.F منیزیم عصبی کاهش منیزیم مغز باشد. وقتی دام بمدت 24 48 ساعت گرسنگی بکشد و یا در هوای بارانی و باد باشد، هورمون آدرنالین ترشح می - شود که هورمون استرس است و دارای اثر لیپولیتیک می - باشد. در نتیجه ذخایر چربی تجزیه میشود. علائم بالینی: بیماری به سه فرم دیده میشود: فرم حاد ⇐ دام از چرا کردن دست می کشد. انقباض و انبساط آنی ماهیچه ها و گوش ها را از خود نشان می دهد و گوشش را مرتباً میچرخاند. دام بسیار تحریک پذیر است و در اثر وارد کردن تحریک نعره می کشد و به این طرف و آنطرف دیوانه وار فرار می کند. همچنین دام دچار دندان قروچه و عدم ت عادل است و روی زمین افتاده و دچار تتانی در دست و پاها میشود. نیستاگموس، ترشح ، opistotonus در این مدت دام دچار کف در دهان، پوشانده شدن چشم بوسیله پلک سوم، انقباض پلک ها )چشمها از حدقه بیرون زده( و سیخ شدن گوشها میشود. بین حملات تشنج، دام کاملاً آرام روی زمین دراز می - کشد ولی در اثر تحریک یا لمس حیوان، دچار تشنج شده و ممکن است در طی یکی از این حملات ،تلف شود. تعداد تنفس و پالس قلبی افزایش می یابد و دمای بدن به علت انقباضات عضلانی ممکن است به 40 تا 41 درجه برسد. این فرم بیماری به درمان خوب جواب میدهد. فرم تحت حاد ⇐ در این نوع بمدت 3 الی 4 روز حیوان کم اشتهایی مختصری را نشان می دهد. سپس حرکات پاهای حیوان ناموزون می شود و دچارعدم تعادل می گردد و در مقابل تحریک برای واداشتن حیوان به حرکت، مقاومت می - کند. حیوان مرتباً سرش را تکان می دهد و تعداد دفعات ادرار و مدفوع افزایش و میزان تولید شیر و حرکات شکمبه کاهش مییابد. دام دچار لرزش عضلانی و تتانی خفیف در پاها است و چفت شدن فک ها) است . تتانی در دام ) Trismus حیوان دچار بصورت خفیف دیده می شود و حیوان سرش را عقب نگه می - دارد. ایجاد صدا یا حرکات ناگهانی و یا لمس دام، منجر به بروز تشنج در دام میشود. حیوانی که علائم فرم تحت حاد را نشان می دهد ممکن است طی چند روز بهبود یافته و یا زمین گیر شده و به فرم حاد بیماری گرفتار شود. این فرم بیماری به درمان جواب می دهد ولی تمایل زیادی به عود بیماری دارد. فرم مزمن ⇐ در تعداد زیادی از دامهای گله، میزان منیزیم سرم کمتر از حد طبیعی است ولی علائمی را نشان نمی دهند. فقط تعداد کمی از دامهای گله علائم مبهمی مثل گیجی، تنبلی، تغیر اشتها و برخی مواقع تعدادی از علائم اصلی بیماری را نشان میدهند. تشخیص تفریقی: بیماری را باید از مسمومیت با سرب، هاری و فرم عصبی کتوز تفریق داد. البته این بیماری می تواند با تب شیر و کتوز بصورت توام بروز نماید. درمان: % الف) تجویز محلول های حاوی منیزیم و کلسیم ( 25 بروگلوکونات کلسیم و 5% هیپوفسفیت من یزیم ). از این CMP و 500 سی سی هم محلول IV محلول 500 سی سی به صورت SC بصورت همزمان تزریق میکنیم ب )تجویز محلول منیزیم ( 20 % سولفات منیزیم) 200 تا 300سی سی از محلول 20 % سولفات منیزیم تزرق می کنیم . چون عیار منیزیم با این IV بصورت ترزیق پس از 3 سا عت در خون کاهش می یابد، بهتر است که SC 200 از محلول 50 % سولفات منیزیم بصورت cc همزمان تزریق شود. ج) محلول منیزیم ( 15 % لاکتات منیزیم) 200 تا 400 سی سی از محلول 25 % لاکتات منیزیم تزریق شود. IV بصورت لاکتات منیزیم بمدت طولانی در خون باق ی می ماند و عیار منیزیم را بالا نگه میدارد. خالی از خطر نیست I.V * تزریق املاح منیزیم بصورت زیرا روی بصل النخاع و قلب تاثیر سوء دارد و می تواند باعث اختلالات تنفسی و مرگ دام شود . در صورت مشاهده چنین عوارضی بلافاصله تزریق منیزیم را قطع می کنیم100 از محلول 10 % از (بروگلوکونات کلسیم را بصورت cc و به دام تزریق میکنیم. IV بهترین روش درمان استفاده از محلول سولفات منیزیم میباشد. پیشگیری: خوراندن املاح منیزیم از بروز بیماری پیشگیری می - کند. 60 اکسید منیزیم بصورت خوراکی (روزانه) gr ← گاو 7 اکسید منیزیم بصورت خوراکی (روزانه) gr ← گوسفنددر مناطق بارانی حتماً برای دام سرپناه در نظر گرفته شود. اضافه کردن کودهای منیزیم به زمین های کشت علوفه و کم کردن کودهای پتاسی. کمبود منیزیم در گوسالهها (Hypomagnesaemia Tetany of calves) میزان منیزیم شیر زیاد نیست ولی به علت بالا بودن قدرت جذب منیزیم، توسط گوساله های شیرخوار، کمبود منیزیم در ابتدا ظاهر نمی شود. ولی با افزایش سن گوساله ها که توام با افزایش نیاز به م نیزیم است، منیزیم شیر کفاف نیازهای گوساله را نمی دهد و دام دچار کمبود منیزیم میشود. گوسالههایی که به کمبود منیزیم حساسترند، عبارتند از: - 1) گوسالههای که فقط از شیر استفاده می - کنند. - 2) گوسالههایی که سرعت رشد بیستری دارند و وزن آﻧﻬا بیشتر است. -3)گوسالههایی که شیر بیشتری میخورند -4) گوسالههایی که بیشتر دچار اسهال می - شوند. -5) گوسالههایی که در زمستان بدنیا می - آیند. -6)گوسالههایی که غذای خوبی به آﻧﻬا داده نمیشود. -7) گوسالههای 2 تا 4 ماهه -8)گوسالههایی که مرتباً مواد فیبروزی بستر خود را میجوند، به علت بروز ترشح بزاق و دفع منیزیم از طریق مدفوع به (Salivation) بیماری حساسترند. علائم بالینی: گوساله مداوماً گوش خود را می چرخاند و حرکت می - دهد. دمای بدن معمولی است ولی با پالس قلب افزایش می - می شود. لرزش عضلانی دارد و Hyperesthesia یابد. دام دچار با پاهای خود به شکمش لگد می زند. قادر به آشامیدن دارد. (Frothy Salivation) آب نیست و بزاق کفآلود همچنین عضلات دستها و پاها و فک دچار انقباض هستند. دام زمینگیر است و سرش را مرتباً عقب می کشد و تعداد دفعات ادرار و مدفوع افزایش مییابد. در گوساله های بزرگتر نیم ساعت پس از شروع علائم، مرگ اتفاق می افتد. ولی در گوساله های کم سن ممکن است دام موقتاً بهبود پیدا کند ولی در حملات بعدی بیماری، دام تلف شود. تشخیص تفریقی: این بیماری را باید از مسمومیت با سرب، و بیماری A آنتروتوکسمی، کمبود ویتامین تفریق (Polio encephalo malacia) PEM پولیوآنسفالومالاسی داد. درمان: 100 cc محلول 10 % سولفات منیزیم به میزان I.V تزریق بمدت یکروز دام را کفایت می کند (چون منیزیم استخواﻧﻬا هم کاهش پیدا کرده است ). باید علاوه بر تزریق سولفات منیزیم از اکسید منیزیم یا کربنات منیزیم بصورت خوراکی هم استفاده نمود که این میران عبارت است از : 1(روزانه) gr 5 هفتگی - 2(روزانه) gr 5 تا 10 هفتگی - 3(روزانه) gr 10 تا 60 هفتگی - اگر از کربنات منیزیم استفاده می کنیم این ارقام را باید دو برابر کنیم. * برای تخفیف علائم تشنج می توان از کلرال هیدرات و دیازپام استفاده کرد. پیشگیری: باید در جیره گوساله ها از اکسید یا کربنات کلسیم و همچنین از یونجه بعنوان بخشی از جیره استفاده نمود.
بیشتر بخوانید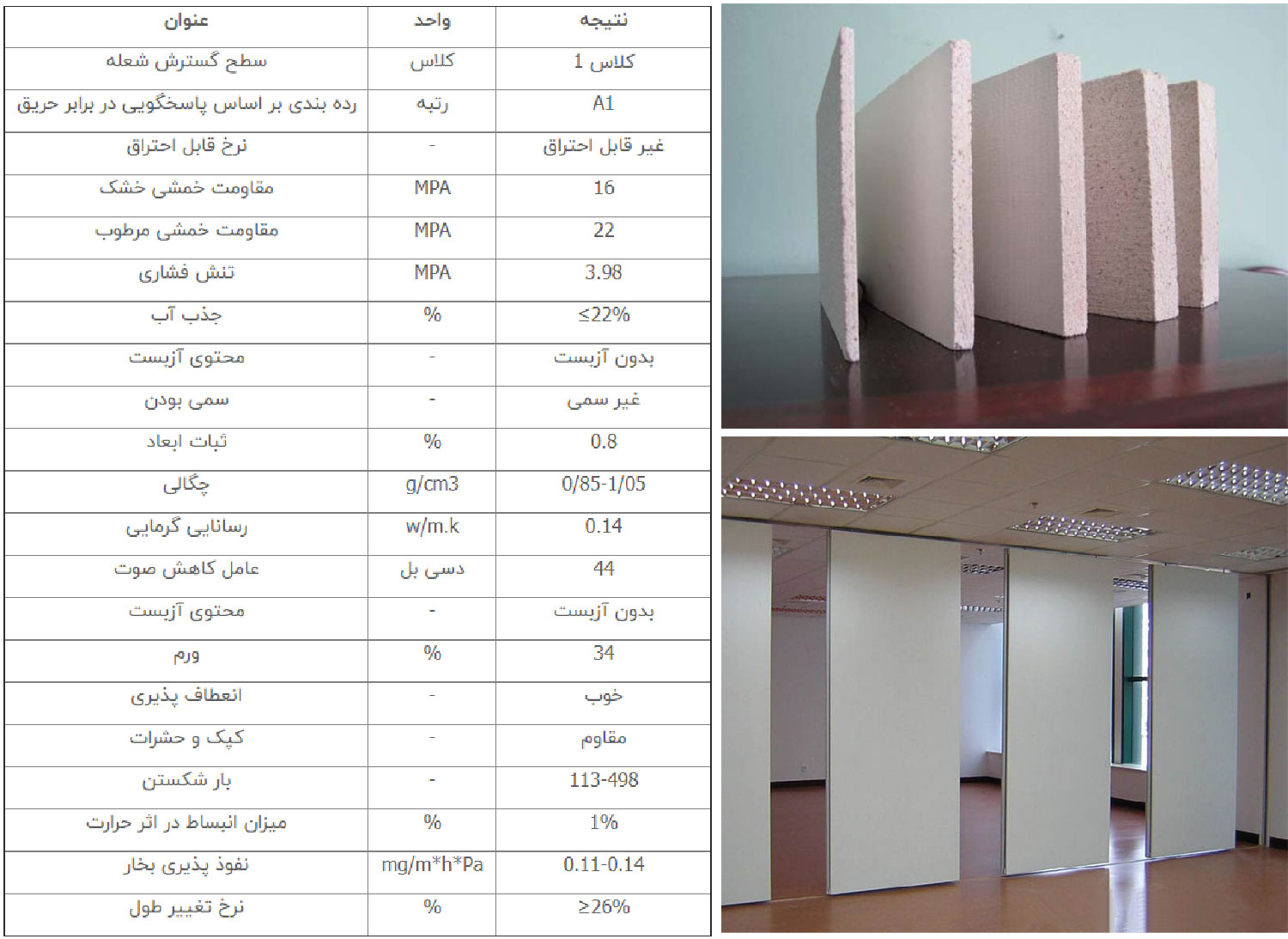
تولید-شمش-منیزیم - منیزیم بورد یا دیوارهای پانل منیزیم یا پانل منيزيم یا بورد منیزیم محصولی است که از ترکیب اکسید منیزیم، کلرید منیزیم و افزودنی های دیگر به صورت ورقه های درحد چند میلیمتر تا سانتی متر ساخته می شوند و امروزه کاربرد آن در صنعت ساختمان سازی و بخصوص برج سازی بسیار حیاتی است. مهمترین مشخصه های پانل منيزيم یا بورد منیزیم عبارتند از وزن سبک، نسوز، محفاظت در برابر اشعه، اجرای سریع و آسان، دستیابی به فضای مفید بیشتر، کاهش وزن ساختمان، عایق حرارت، برودت، صدا، رطوبت، مقاوم در برابر حشرات, آنتی باکتریال و ضد کپک زدگی اداوه مطالب از لینک زیر> https://kargosha.com/fa/content/id/500/%D9%BE%D9%86%D9%84-%D9%87%D8%A7%DB%8C-%D8%A7%DA%A9%D8%B3%DB%8C%D8%AF-%D9%85%D9%86%DB%8C%D8%B2%DB%8C%D9%85-(MgO-Boards) اکسید منیزیم یک ماده ی معدنی تطبیق پذیر است که هنگامی که به عنوان بخشی از یک مخلوط سیمانی مورد استفاده واقع شده و وارد یک روند عمل آوری مناسب و ممارست در این روند شود، به شکل پانل های سیمانی نازکی قالب ریزی می شود که این محصول در صنعت ساخت و ساز مورد استفاده قرار می گیرد. پنل های اکسید منیزیم یا (MgO Boards) محصولی است سازگار با محیط زیست از نوع پنل های پوششی که به صورت پیش ساخته و فاقد عایق است که جایگزینی است برای کلیه پنل های پوششی گچی، سیمانی و چوبی و می توان آن را در بخش های مختلف ساختمانی، از جمله کف، سقف، دیوار و نما مورد استفاده قرار داد. مقاومت و استحکام قابل ملاحظه این محصول به دلیل وجود پیوند بین اتم های منیزیم و اکسیژن که مولکول اکسید منیزم را شکل می دهد، است. لازم به ذکر است که در صورت کاربرد این محصول به صورت ترکیبی با مواد عایقی همچون XPS، ESP، پشم سنگ، فوم پلی اورتان و فایبر گلاس می تواند عایق حرارتی، صوتی یا رطوبتی مقاوم تری ایجاد گردد. در مقایسه این محصول با محصولات مشابه، پنل های اکسید منیزیم ازDry Wall سخت تر هستند و به نوعی شبیه سمنت برد ها هستند. این محصول به گونه ای که ترکیبی از عملکرد Dry Wall و سمنت برد است عمل می کند. لذا این ذهنیت در مورد ورق های اکسید منیزیم وجود دارد که آنها نوعی ورق پوششی همانندDry wall یا سمنت برد ها می باشند اما در حقیقت خواص بسیار پیشرفته تری را دارا هستند. از آن جمله می توان به مقاومت حرارتی بالای این محصول، قابلیت عدم فرسایش در مجاورت هوا، استحکام بالا و مقاومت در برابر قارچ و کپک را نام برد. پنل های اکسید منیزیم در فرم های گوناگونی یافت می شوند و ابعاد و ضخامت های متفاوتی را بسته به اینکه مورد استفاده چه بخشی از ساختمان قرار می گیرند، دارا هستند. رتبه های متفاوتی نیز برای این محصول در نظر گرفته شده است. از آن جمله می توان به سطوح نرم، بافت زبر و رتبه های کاربردی متفاوت آن اشاره نمود. این محصول در سه رنگ سفید، خاکستری و بژ یافت می شود و اکثر کارخانه های تولید کننده این محصول در آسیا واقع هستند. پنل های اکسید منیزیم از پنج لایه اصلی تشکیل شده اند: لایه سطح رویی یا بیرونی لایه شبکه ی فایبر گلاس تقویت شده که باعث استحکام و مقاومت ورق می شود.پنل های اکسید منیزیم لایه پر کننده (شامل عامل چسبانده ی منیزیم به سیمان، پرلیت و خاک اره). لایه دوم تقویتی از شبکه ی فایبر گلاس لایه پر کننده سطح پشت ورق مزایا: این ورق ها بسیار سبک هستند. در برابر ضربه،حریق، رطوبت، و نفوذ حشرات مقاوم است. ضد کپک و ضد قارچ است. بدون گرد و غبار سمی بوده و لذا سرطان زا نمی باشند. به ابزار خاصی جهت برش نیاز ندارد. در تمامی اجزای ساختمانی، دیوار های درونی و بیرونی، کف و سقف به صورت ترکیبی قابل کاربرد است. این محصول سبز بوده، دوستدار محیط زیست بوده و قابل بازیافت است. معایب: مواد خام جهت تولید این مصالح در چین موجود می باشد و دولت های محلی چینی صادرات این مواد خام را متوقف کرده اند. لذا این جزء مصالح بومی نیست. همانند همه ترکیبات سیمانی، سیمان های منیزیمی نیز در طی مراحل عمل آوری و پخت مستلزم مراقبت زیاد و همچنین صرف وقت و هزینه ی زیادی است. لذا بسیاری از برند های دیگر وجود دارند که محصولات خود را با قیمت پایین تر و قابلیت آماده سازی آسان تر عرضه می کنند. پنل های اکسید منیزیم شیوه منحصر به فردی در نصب دارند و نیاز است که برای جلوگیری از بروز مشکل هنگام نصب با استفاده از توصیه های کارخانه کار دنبال شود. بسیاری ار این پنل ها با سیمان سورل (Sorel Cement) محافظت می شوند که این نوع سیمان قدرت زیادی در رطوبت دارد و در صورت نصب این مصالح در مناطق مرطوب پدیده ای در این مصالح رخ می دهد که به «ورق گریان» معروف است به طوریکه از پانل ها قطرات آب می چکد. کلرید موجود در این مصالح محیطی خورنده برای چفت ها و استاد های فلزی که این مصالح را نگه می دارد ایجاد می کند. موارد استفاده: در فضاهای داخلی و خارجی ساختمان ها با کاربری گوناگون به عنوان روکش خارجی مصالح به عنوان پوشش خارجی دیوار های داخلی و سقف به عنوان دیوار جدا کننده یا پارتیشن در بخش های داخلی ساختمان در جایی که عایق ضد حریق و عایق ضد رطوبت مورد نیاز است در جایی که سطح بالایی از عایق صوتی مورد نیاز است مانند استودیو های صدا برداری در جاهایی که استفاده از مصالح ضد حریق ضروری است مانند مراکز خرید در جاهایی که به مصالح با استحکام بالا و مقاوم در برابر زلزله نیاز است مانند مدارس و هتل ها اجرای سقف و کف های کاذب ساختمانی به عنوان پوشش نهایی نما به عنوان پوشش محافظ زیرین تایل ها و کف به عنوان دیوار های داخلی، خارجی، کف و سقف ساختمان های پیش ساخته با اسکلت فلزی در صنعت تولید اثاث منزل، مانند کمد، قفسه، کابینت و... ، جایگزینی برای MDF و HDF در ستون، طاق، زیر طاق در صنعت کشتیرانی، هواپیماسازی، صنایع نظامی و ... پارتیشن بندی قطار ها و اتوبوس ها در طیف گسترده ای از کاربری های مختلف، تجهیزات پزشکی و جلوگیری از نفوذ اشعه ی X-Ray. ساخت فضا های خنک مانند سردخانه ها وش نصب و اجرا: پنل های اکسید منیزم را می توان به آسانی علامت گذاری کرد، با ابزار های متعارف برید، کوتاه کرده و شکل داد. آنها قابلیت دریل شدن، اره شدن و نصب شدن بر روی قاب های فلزی (عضو مخصوص نصب این مصالح) را دارا می باشند. سیستم های متفاوتی برای نصب این پنل ها بسته به شرایط وجود دارد که بهترین روش Dry wall می باشد. هنگام انبار کردن این مصالح باید مد نظر داشت که این مصالح بر روی سطح صاف و مسطح انبار شوند. همچنین می بایستی این اطمینان حاصل شود که کلیه ی ورق ها با پوشش و در جای خشک انبار می شوند. چنانچه ورق ها مرطوب باشند قبل از نصب بایستی خشک شوند در هنگام حمل بایستی ورق ها به صورت عمودی حمل شوند، حمل افقی ورق ها باعث ایجاد خمش و شکستن ورق ها می شود. الزامات نصب: ترکیب این مصالح با عایق صوتی و حرارتی در هنگام استفاده به عنوان دیوار بین واحد ها یا دیوار های خارجی به کیفیت کاربردی این مصالح می افزاید. مهار بندی قائم، بنا به توصیه ی آیین نامه، در اجرای این مصالح برای دهانه های وسیع و قاب های ساختمانی بزرگ بسیار موثر است. در هر مرحله از نصب بایستی تراز کنترل شود. پیچ ها به صورت زیگزاگ و تا حد ممکن محکم نصب شوند. این امر به افزایش مقاومت برشی و جلوگیری از لق شدن و افتادن پنل ها کمک می کند. تا حد ممکن پیچ در نیمه ی سمت جان پروفیل نصب شود. این امر از خم شدگی پروفیل نگهدارنده پنل توسط پیچ جلوگیری می کند. دقت شود تا در اتصال این سازه به دیوار آجری، پیچ با دیوار درگیری کامل برقرار کند. از رول پلاک یا چسب های مخصوص ساختمانی می توان جهت درگیری بهتر در دیوار های سست استفاده نمود. محل رسیدن لبه ی پنل ها به یکدیگر بایستی بر روی سازه قرار بگیرند. سازه نگهدارنده ورق ها از طرف عرضی حداقل دو قسمت و از طرف طولی حداقل سه قسمت از ورق را بایستی پوشش دهد. تنظیم فواصل بین این سازه های نگهدارنده بایستی به گونه ای باشد که اثرات مکش یا فشار باد خنثی شود. اتصالات نبایستی از 51 میلیمتر از گوشه به یکدیگر نزدیکتر باشند و از همان گوشه با پیچ مجاور نبایستی کمتر از 102 میلی متر فاصله داشته باشند. انتهای پنل ها بایستی با اتصالات تقویت شود. در صورتی که سازه ی پشتیبان از مقاطع چوبی شکل گرفته است، بایستی تمهیدات لازم برای جلوگیری از نفوذ حشرات خورنده و پوسیدگی اعمال شود. بسته به ضخامت و وزن پنل ها، فواصل بین پیچ ها برای جلوگیری از برش پانچ بین 15 الی 25 سانتی متر متغیر است. دقت شود تا در هنگام پیچ کاری سر پیچ با سطح پنل همباد شود. در کلیه ی شکستگی ها و زوایا استفاده از توری مش کرنربید توصیه می شود. فوم سایلنس ضد ارتعاش صوت، در زیر محل پیچ ها در محل هایی که کاهش حجم صوت مد نظر است مورد استفاده قرار می گیرد. چنانچه مقاومت در برابر حریق مد نظر باشد، می توان با دو لایه نمودن پوشش ورق ها به طوریکه اولا رعایت حصیر چینی در اجرای ورق ها رعایت شود، و ثانیا اتصال پیچ ها باعث کاهش مقاومت برش پانچ ورق ها نگردد اقدام نمود. در اجرای دیوار های پیرامونی با این پنل ها بهتر است از دو لایه ورق به صورت حصیر چینی استفاده شود. چنانچه از این مصالح در مناطق مرطوب، مانند سرویس بهداشتی یا آشپز خانه استفاده می شود بایستی به درز بندی کامل توجه شود تا از نفوظ رطوبت به لایه های زیرین کار جلوگیری شود. از اتصال این پنل ها به صورت مرطوب بایستی خودداری کرد. اتصالات همواره بایستی به همراه بخش های سازه ی تقویتی نصب شود تا امکان اتصال تایل های سرامیکی بر روی این مصالح فراهم باشد. چه رنگ روغنی باشد چه رنگ پلاستیک، همواره بر روی این پنل ها قابل استفاده استپوشش های رویی این پنل ها را با اتصالات پیچی متحرک نصب نکنید، مگر اینکه بر روی سازه ی تقویتی نصب شود.
بیشتر بخوانید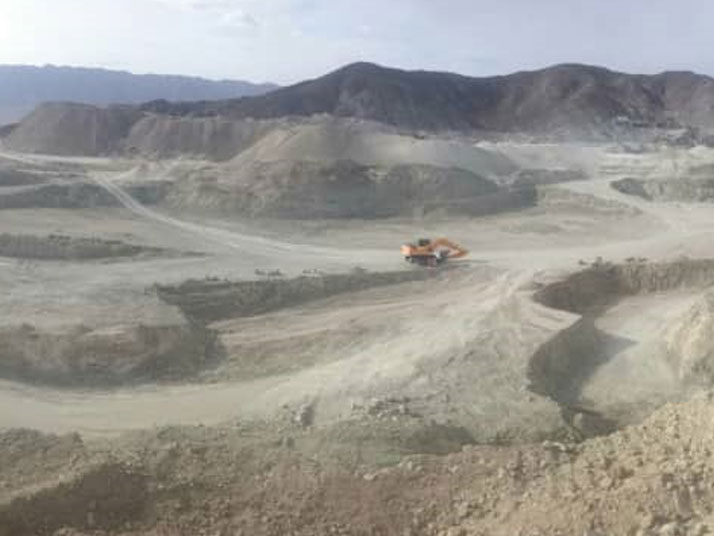
این معدن در شمالغرب شهرستان نهبندان واقع شده است و با ذخیرهای بالغ بر 500هزار تن (قطعي و 1ميليون و_
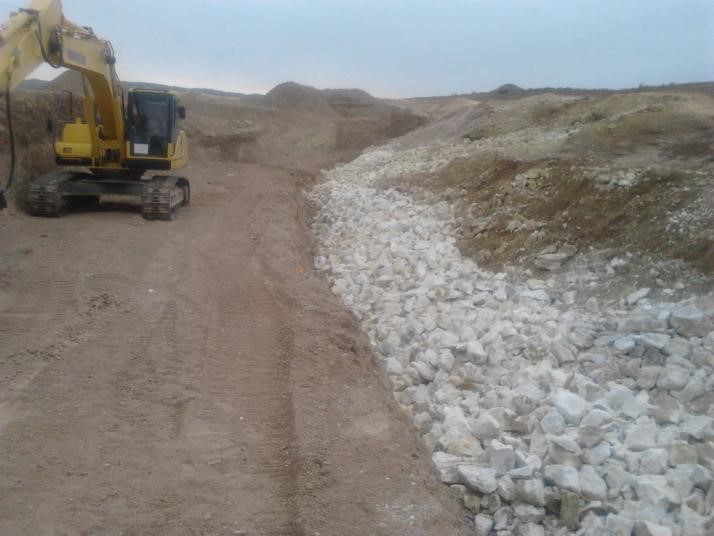
این معدن نیز در شمال نهبندان واقع شده و حدود 200000 تن ذخیره دارد. در حال حاضر عملیات اکتشافی بر روی_

خبرهای 2025